Projects
BROWNFIELD DEVELOPMENT
Brownfields are all about making the environment safe for people.
Gates Rubber Company Property Redevelopment, Denver, Colorado
As advisor to the purchaser of one city block of the former Gates Rubber Company manufacturing complex, Slosky & Company conducted soil, soil gas, groundwater, and building materials testing for the demolition of three manufacturing buildings. Assistance was provided in obtaining a No Further Action letter from the state environmental agency. Construction is currently underway on the mixed-use commercial and residential structures.
Ninth Square Historic Redevelopment, New Haven, Connecticut
Slosky & Company assisted legal counsel in conducting the environmental due diligence and remediation planning for an $86.6 million downtown redevelopment in New Haven, Connecticut. The review included Phase I assessments, asbestos testing, soil-gas testing, soil and groundwater testing, and lead-based paint and radon testing. Slosky & Company developed construction/completion protocols for asbestos, lead-based paint, and petroleum-contaminated soils. The mixed use residential and commercial project was successfully completed with extensive remediation conducted concurrently with construction activities.
Redevelopment of the NASA Industrial Plant, Downey, California
Slosky & Company provided environmental due-diligence services and testing for the acquisition of a portion of the 140-acres National Aeronautics and Space Administration (NASA) industrial plant (NIP) in Downey, California. The site is located approximately 15 miles south of downtown Los Angeles.
NIP was used for aerospace and aircraft design and manufacturing starting in the late 1920s. The Apollo and Space Shuttle Orbiter components were manufactured and maintained at this facility. This facility housed the first operating nuclear reactor in the state.
Slosky & Company services included the review of historic operational documentation, environmental assessments including soil and groundwater testing conducted by the government, ongoing remedial activities, and regulatory compliance issues. Slosky & Company also conducted soil testing on the site.
Denver Radium Site Redevelopment, Denver, Colorado
Environmental due diligence services were provided by Slosky & Company for the acquisition and development of a portion of the Robinson Brick Company (ROBCO) Denver radium site. The site was the location of a radium processing facility established by the National Radium Institute. ROBCO later acquired the property and used it as a brick and tile manufacturing site from approximately the 1940s to the mid-1980s. The site was on the National Priorities List. Radiological and non-radiological assessment and remediation have been performed at the site.
Assessment of Contaminated Soil Volumes at Former Rail Yard, Las Vegas, Nevada
Slosky & Company personnel resolved inconsistencies in environmental measurements at a former rail yard undergoing remediation to commercial/retail land use standards.
By adapting the statistical techniques of Youden & Steiner, it was demonstrated that alternative field screening data for lead in soils by x-ray fluorescence bettered performance of fixed laboratory data. Reduction in the amounts of soil requiring remediation yielded cost savings to the client of approximately $1 million. Case study was published by USEPA and the Air & Waste Management Association, 1993.
Radioactive Waste Screening at Residential Development Site, Denver, Colorado
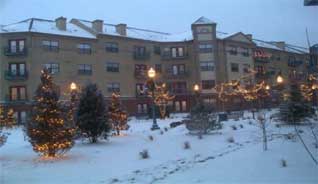
A luxury residential development was constructed near a Denver Radium National Priorities List site in the Central Platte Valley of Denver. Slosky & Company developed, gained government approval of, and implemented a site-specific health and safety plan to protect workers from radiological hazards and screened excavated soil to identify any radioactive soil remaining. The firm also remediated areas contaminated by petroleum and asbestos.
Environmental Due Diligence and Management for Residential Redevelopment, Jersey City, New Jersey
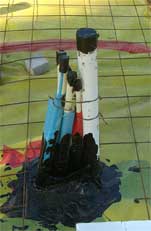
Slosky & Company advised the major investor in the environmental due diligence, development, and implementation of a remedial action plan implemented under a state administrative order in Jersey City, New Jersey. Contaminants included lead-contaminated soil and chlorinated solvents in the groundwater. Remedial activities included a soil cap over the entire site and vapor barriers in buildings over the contaminated groundwater. Construction was successfully completed.
Cupples Station Westin Hotel Redevelopment, St. Louis, Missouri
Slosky & Company advised the major investor in the due diligence and remediation of a portion of the Cupples Station warehouse district. Remediation was conducted under Missouri’s voluntary cleanup program on rehabilitated warehouse buildings. Environmental activities addressed lead and petroleum contaminated soil; asbestos and lead-based paint abatement.
Former Brick and Furniture Manufacturing Facility, Los Angeles, California
Slosky & Company advised the major investor in the assessment and remediation of the site with solvent contamination of the groundwater and lead contamination of the soil. Lead levels in the soil exceeded 50,000 ppm. Slosky & Company spared its client most of the costs for a 23-week $4 million cleanup.
Legends Park and University Place Revitalization, Memphis, Tennessee
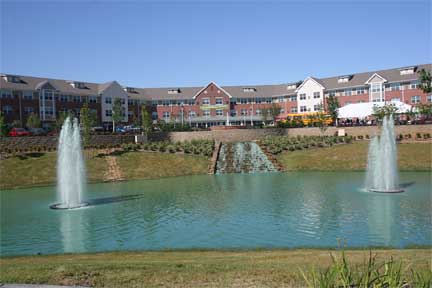
From project initiation to receipt of No Further Action (NFA) decisions, Slosky & Company advised multiple developer partners and investors on the successful transition of a formerly industrialized area to residential land use. The firm provided leadership and guidance to local consultants regarding environmental matters for which local regulatory oversight had not yet promulgated regulations or guidance. Slosky & Company established a collaborative relationship with state regulators, allowing issuance of pre-NFA interim status letters to facilitate financing in an increasingly tight credit market. Construction is currently underway.
Mississippi River–Gulf Outlet Remediation, New Orleans, Louisiana
As project manager for completion of a 5-year $30 million human health and eco-risk based brownfields remediation with a budget to complete of $4.6 million, Slosky & Company personnel negotiated cost-saving alternatives totaling approximately $1 million with the client and regulatory oversight (Louisiana and USEPA Region VI). Multiple No Further Action decisions were obtained from state oversight for formerly industrial properties remediated to residential use levels. The project was completed on time and on budget. Site soils were classified as sufficiently clean to allow their re-use at post-Katrina levee reconstruction projects by the U.S. Corps of Engineers.
Evaluation of Allegedly Explosive Radioactive Waste Tanks, Denver, Colorado
Slosky & Company personnel led technical presentation with the Colorado Department of Public Health and the Environment and Colorado Attorney General’s office regarding a pending consent decree for management of allegedly explosive radioactive hazardous waste storage tanks, reporting to two corporate general counsels.
Containment of Pesticide & Nerve Gas Residues, Rocky Mountain Arsenal, Denver, Colorado
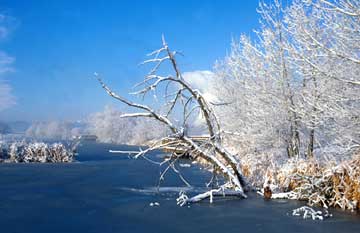
Slosky & Company personnel designed chemical compatibility testing protocols for slurry wall materials proposed for use during remediation of Rocky Mountain Arsenal’s Section 36. Approach was negotiated with state and federal regulatory oversight. Approval was obtained for use of chemical surrogates in treatability testing; thus reducing chemical exposure potential of pesticide/nerve agent derivatives for geotechnical laboratory personnel. Results were published in
Soils, Sediment, and Groundwater, Innovative Technologies, 2000.
Assessment of Radiologically-Contaminated Asbestos, Rocky Flats, Denver, Colorado
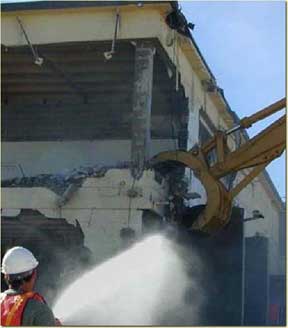
Slosky & Company personnel designed a radiological characterization plan for plutonium-contaminated asbestos, meeting requirements of the Nevada test site as well as the Department of Transportation. Alternative approach eliminated the need to route 55-gallon drums through a radioactivity counter, allowing for more efficient packaging in 40-cubic-yard containers. Cost savings for the packaging and disposal operation approached $3.7 million. Described in
Breaking New Ground for Asbestos Assaying and Shipping by Jeanna Blatt, Rocky Flats Envision, Vol. 8, No. 2, 2002.